Some Known Incorrect Statements About Alcast Company
Some Known Incorrect Statements About Alcast Company
Blog Article
Rumored Buzz on Alcast Company
Table of ContentsHow Alcast Company can Save You Time, Stress, and Money.Getting The Alcast Company To WorkThe Facts About Alcast Company UncoveredWhat Does Alcast Company Mean?What Does Alcast Company Mean?The Best Strategy To Use For Alcast CompanyWhat Does Alcast Company Mean?Some Of Alcast Company
It possessed good strength and machinability. There are several other aluminum alloys that can be used for casting components. To learn which alloys would benefit your projects, call Impro.
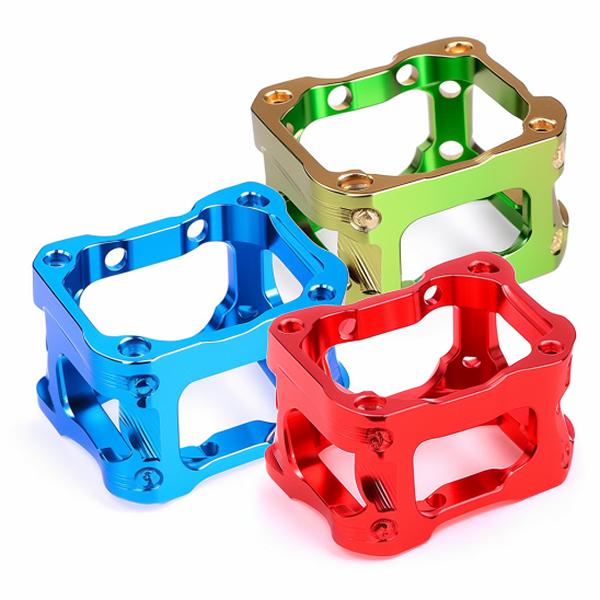
Different aspects and quantities create a wide array of preferable physical and chemical residential properties. And the Aluminum Organization (AA), based in The United States and copyright, has developed specs that manage light weight aluminum alloys' structure, properties, and nomenclature. There are two kinds of aluminum alloys functioned and cast. Foundry employees create these alloy kinds in various means, which significantly affects their features.
Alcast Company - An Overview
Cast light weight aluminum alloys are made by thawing pure aluminum and integrating it with various other metals while in liquid type. The mix is put right into a sand, die, or financial investment mold. After solidification, the steel is gotten rid of from its mold and mildew. At this stage, it remains in either its final type or as a billet or ingot for further processing.
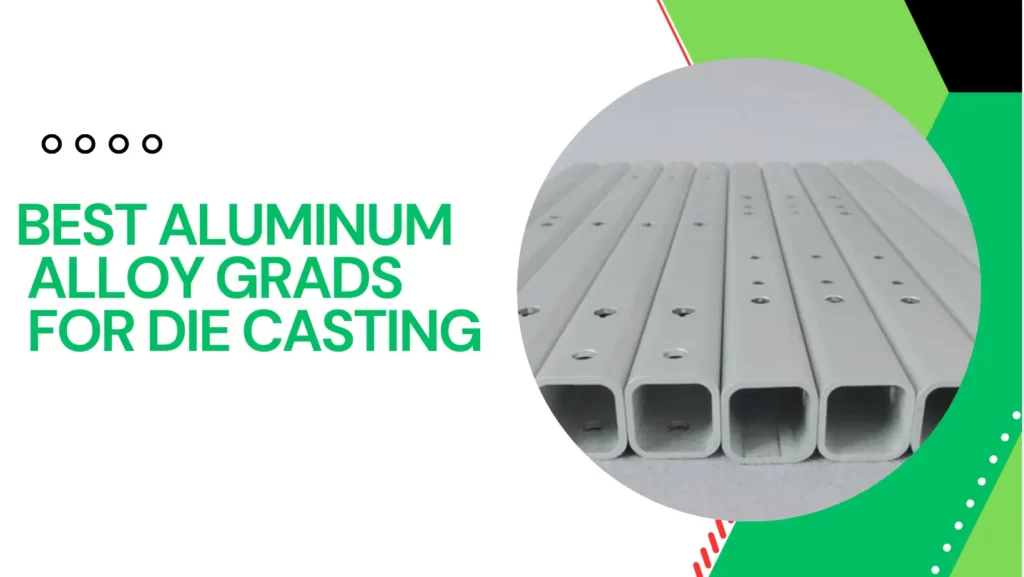
There are several small differences between functioned and cast aluminum alloys, such as that actors alloys can have much more significant amounts of various other metals than wrought alloys. But the most notable difference between these alloys is the manufacture procedure where they will certainly most likely to supply the last item (aluminum metal casting). Apart from some surface treatments, cast alloys will exit their mold and mildew in nearly the exact solid type desired, whereas wrought alloys will go through numerous adjustments while in their strong state
4 Easy Facts About Alcast Company Shown
If you assume that a functioned alloy may be the very best for your job, have a look at some of our short articles that clarify more about particular wrought alloys, such as Alloy 6061 and Alloy 6063. On the various other hand, if you assume an actors alloy would be better for you, you can discover much more concerning some cast alloys in our Alloy 380 and Alloy 383 short articles (coming soon).
When selecting an aluminum shop for your production requirements, it's critical to study numerous variables. One of the most crucial elements to take into consideration is the experience and capability of the foundry. Choosing a foundry that has the best understanding of the light weight aluminum casting procedure, and the portfolio to reveal for it, helps to have an effective outcome for your task.
The Facts About Alcast Company Revealed
Having the experience and market understanding to craft your spreadings for ideal manufacturing and top quality outcomes will certainly streamline the project. Making light weight aluminum castings needs a complicated collection of procedures to attain the best outcomes. When making a decision on a brand-new aluminum shop to partner with, guarantee they have substantial market experience and are educated concerning all elements of the light weight aluminum spreading procedure: design, production, product analysis, and item testing.
The factory must also have a proven track record of delivering phenomenal products that meet or go beyond client expectations. Quality assurance ought to likewise be at the top of your listing when choosing an aluminum shop. By functioning with a qualified factory that follows the criteria for high quality control, you can protect the stability of your item and ensure it fulfills your requirements.
How Alcast Company can Save You Time, Stress, and Money.
By picking a company that supplies solutions that fulfill or exceed your product requirements, you can be sure that your task will be finished with miraculous accuracy and effectiveness. Particular light weight aluminum foundries focus on details types of making processes or casting techniques. Various parts require various production strategies to cast aluminum, such as sand casting or die spreading.
Die casting is the name offered to the process of creating intricate steel elements with usage of molds of the element, likewise known as dies. It generates more components than any various other process, with a high level of accuracy and repeatability. There are 3 sub-processes that drop under the group of click to read more die spreading: gravity die casting (or long-term mold and mildew spreading), low-pressure die casting and high-pressure die casting.
Alcast Company Can Be Fun For Anyone
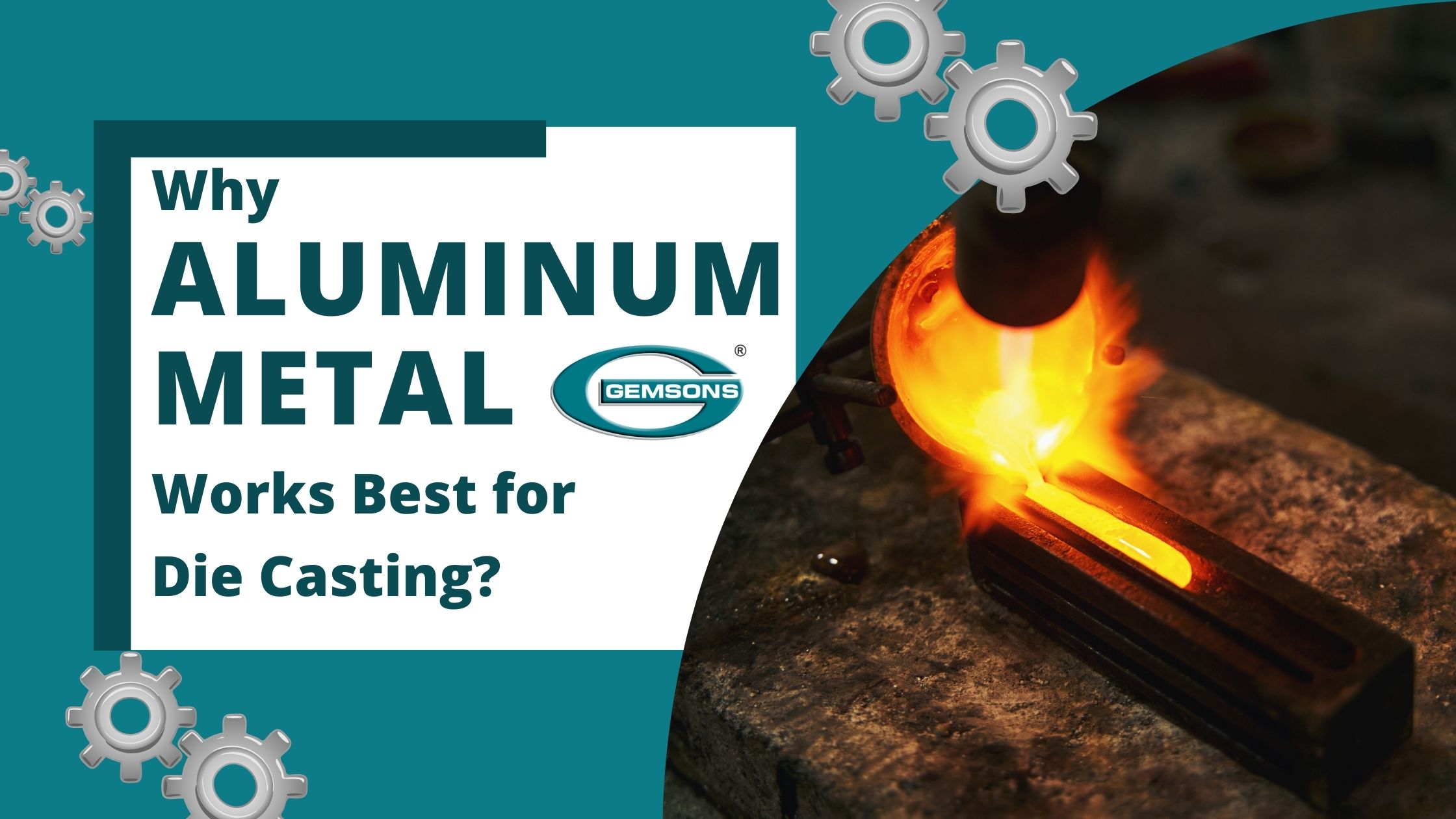
The pure metal, likewise recognized as ingot, is added to the heater and kept at the molten temperature level of the steel, which is then transferred to the injection chamber and infused right into the die. The stress is after that kept as the steel strengthens. As soon as the steel solidifies, the cooling process starts.
The thicker the wall of the part, the longer the cooling time as a result of the amount of indoor steel that likewise needs to cool. After the element is completely cooled down, the die cuts in half open and an ejection system presses the element out. Adhering to the ejection, the die is shut for the next injection cycle.
The Facts About Alcast Company Revealed
The flash is the additional product that is cast during the process. This must be trimmed off making use of a trim tool to leave simply the main part. Deburring removes the smaller sized pieces, called burrs, after the trimming procedure. The element is polished, or burnished, to provide it a smooth surface.
This proved to be an unreliable examination, since the tester can reduce into an item and miss an area with porosity - aluminum metal casting. Today, leading makers use x-ray testing to see the entire inside of parts without cutting into them. This permits them to much more accurately approve or reject parts. To get to the ended up product, there are 3 primary alloys made use of as die casting product to pick from: zinc, aluminum and magnesium.
Zinc is among one of the most pre-owned alloys for die spreading because of its lower expense of resources. It's also among the more powerful and stable steels. And also, it has outstanding electric and thermal conductivity. Its deterioration resistance also allows the elements to be lengthy lasting, and it is among the extra castable alloys due to its reduced melting factor.
See This Report on Alcast Company
As pointed out, this alloy is just one of one of the most typically utilized, yet makes will, sometimes, choose aluminum over zinc due to aluminum's manufacturing advantages. Aluminum is highly cost-effective and one of the more versatile alloys. Light weight aluminum is made use of for a number of different items and sectors anything from window frames to aerospace materials.
Report this page